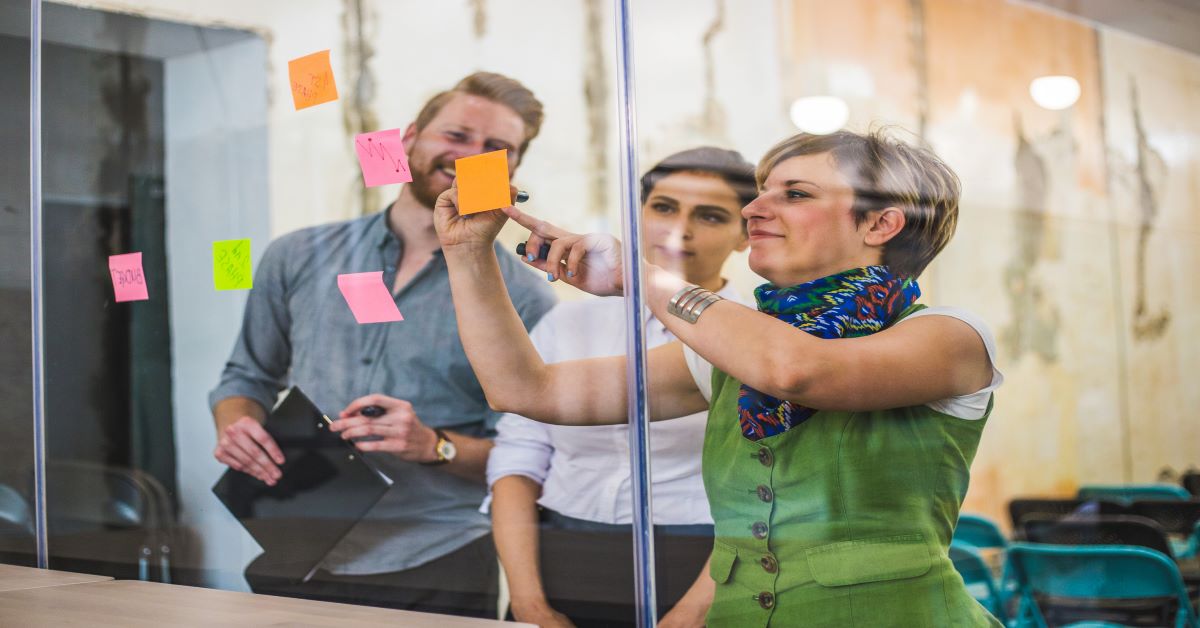

We have spent the better part of the last 25 years continually perfecting state-of-the-art asset management software tools and practices. We’ve focused on the unique test equipment environment. We help companies increase asset utilization, reduce calibration expense and improve compliance. Asset management is where we spend all of our time thinking, inventing, and investing. It is our core competency. Our capabilities help customers accelerate time-to-market and drop costs significantly using proprietary algorithms.
- 400% Increases to Utilization
- 25% to 75% Reductions in Equipment Spend (more typically the capital saved is invested in new growth capital & capabilities)
- 25% to 50% Support Cost Savings (reduced calibration, maintenance, and repair costs)
- 30% time savings
Listen as our customer explains the successes he achieved at 27:48 of the video, Digital Transformation: Asset Management 5.0. We think if you do you’ll want to watch the rest of the video to see how we partnered with our customer to achieve these results!
Calibrations Systems aren’t Designed to Significantly Reduce Calibration Costs
“Add on” asset management capabilities provided by calibration, rental, and other companies, for whom asset management is not a core competency, can not match the cost and speed outcomes our software platform enables. Saving companies money at the expense of their service revenue growth is also not in their interest. In the same way, our solutions can’t compete with world-class rental and calibration services. We don’t even try. It’s our job to leverage those world-class calibration solutions to accelerate processes and keep costs low. We do this using Scireo aEAM.
Our Asset Management Solutions Can be Easily Integrated
Scireo aEAM establishes a common interface for users of test equipment as well as those planning the use, reuse, maintenance, calibration, disposal of, or investment in assets. Our interfaces are purpose build for the user to do their job, whether it’s scheduling the use of owned or rented equipment, reporting utilization, identifying capacity constraints, or being notified of maintenance issues in a test cell. We have customers who use our asset management software across many different sites and which connect to multiple different vendors’ software.
The Big Move: Increase Utilization and Reduce Calibration Expense, Improve Compliance, and Increase Speed
The big move is not at all obvious but is, without a doubt, high leverage. We increase utilization by ending many different forms of hoarding. We embed proprietary algorithms that help reduce calibration expenses.
It is beyond the scope of this post to get into all the details about how we increase utilization. The simple answer is we increase equipment sharing but, as most insiders know, increasing sharing is not so easy given today’s dominant culture of hoarding. We’ve published plenty of other blog posts about this phenomenon so I won’t address it in this one. The blog posts include: Stop Hoarding, Start Collaborating, Accelerate Results; That One Bad Habit That Costs Your Team Millions or Equipment Utilization: What’s Your Number…to name a few.
Increasing Utilization Drastically Increased Performance:
Improved Cost – Up to 50%
When hoarding ends, sharing and collaboration begin, and equipment utilization increases. This will also reduce calibration expense, often by as much as 30% to 50% over time. This is only one benefit in a long line of benefits like improved compliance/quality, speed & responsiveness.
Improved Compliance/Quality — Up to 75%
Our practices ensure we maintain close to 99% database accuracy which is the standard required to produce significant increases to utilization, which we also measure. The strategy to increase asset utilization includes disposing of assets that are underutilized. The selection of which assets are best to dispose of will drive quality and compliance if done properly. Between Sente’s database — where we track obsolescence, equipment downtime, repair, maintenance, out-of-compliance statuses, use, and demand — and the detailed calibration information available from calibration databases, the “bad actors” can be eliminated and the risk of poor measurement quality with them.
Improved Speed & Responsiveness — Improved 2X to 3X
The methods used to end the hoarding culture end it everywhere, including calibration services. Lab services are hoarded with unnecessary ASAP or immediate requests that produce a vicious cycle that is difficult for any calibration lab to cope with.
They end the vicious cycle of…
- Unnecessary ASAP calibration requests driving short-term capacity constraints or higher costs…
- Users continually checking the status with the lab sap their capacity further…
- Responsiveness decreases meaning…
- More ASAP requests…
- and the cycle continues
Overall customers reduce the amount of time their equipment is away from the bench by over 50% and often can get a replacement if they need one. Calibration labs can free more than 25% to be applied strategically with new services to their customers.
Improving Calibration Lab Efficiency
This is not our offer but there are many synergies between these kinds of solutions and our own. These solutions also reduce calibration expense, but not as dramatically. Companies like Indysoft have years of experience helping their customers — either internal calibration labs or 3rd party vendors — increase their efficiency. Connections between our database solutions and calibration management software solutions can produce great value. Some of the strategies used to increase the efficiency of calibration labs are:
- Process automation
- Calibration automation
- Optimization of calibration intervals
- Technical controls in the lab for regulatory of government-mandated requirement
Let Scireo aEAM Accelerate Results for Your Team!
We’re happy to engage you in a conversation and can bring needed expertise into the conversation depending on your situation and potential ROI.
Request a Demo
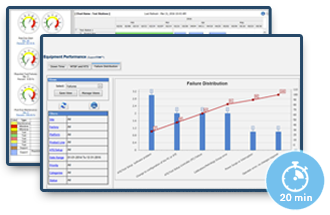
See how Scireo aEAM Software drops asset and support costs by 50% while accelerating time-to-market 2X.
Relevant Content
Reduce Calibration Costs, Increase Quality & Speed!
Most people understand the importance of calibrated equipment to quality measurements and most people think it costs too much. It actually does, probably by 25% or more, which is why so many companies have projects to reduce calibration costs. Those costs aren’t high because your calibration supplier’s cost per calibration is too high or quality…
Drive Test Equipment Utilization to Enable Investments
Driving test equipment utilization is critical to meeting today’s competitive challenges. Freeing up capacity for innovation and growth has never been more important. Companies are being asked to bring products to market in half the time and reduce their cost of operations up to 50% to succeed against aggressive global competitors. In hi-tech manufacturing businesses,…
Case Study: Leading Defense Manufacturer Drives Asset Reduction
See how a Blueprint-for-Action baselined their situation and rapidly installed Scireo suite. It enabled a 50% reduction in obsolete equipment, provided equipment for their growing workforce and solved their compliance challenges.
Equipment Utilization Case Study: Broadband Service Provider
The company was growing double digits but needed to free up investment from operations for growth projects. See how they tripled utilization, freed up capital and resources to enable that investment.
Notable Quotes
“Sente’s Scireo® solution sets a new benchmark in customer experience by increasing collaboration and communications among all participants of a test program. They drive cycle time and cost efficiencies, optimizing asset utilization and technical labor productivity.”
Frost & Sullivan Analyst