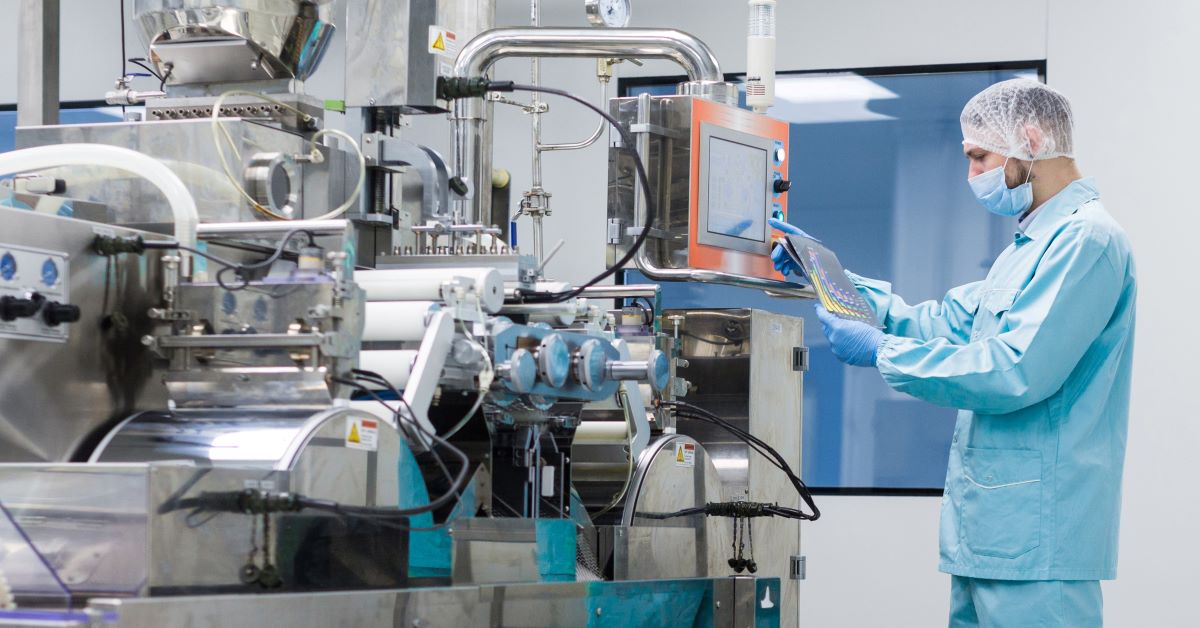

Any complete definition of “Production” must include work that supports the making of some thing or service. That inclusion opens up “production” to include everyone’s work – it really includes your company’s whole supply chain. Wherever work is done is some form of production environment. If that environment (e.g.: computer, truck, instrument, lab space, test cell, workbench, etc.) isn’t available to the worker, they can’t produce. They are ineffective, no production occurs.
Rethinking Production
Too often, however, the term “production” is only used for those activities that produce inventory that is for direct sale. As such, “production” environments get a lot of attention and budget to ensure that those environments are available to produce inventory that will be readily available for sale – having a positive effect on near-term revenue. This way of thinking puts artificial constraints on a business’s use of capital to ensure that their production environments produce a consistent revenue stream now AND into the rapidly changing future. It focuses the use of capital on the near-term revenue stream fed by inventory, not the future revenue stream fed by the design of new innovative products.
Rapidly Changing Markets, Technologies, and Customer Requirements
Of course, the manufacturing environments that have traditionally been deemed “production” need to be available for revenue generation – now and always. If you can’t ship your product, you can’t produce revenue and nothing good ever happens when revenues decrease. That said, in our current rapidly changing environment, having a steady stream of new product innovations intending to be first to market requires a different way of thinking about those other “production” environments – specifically the environments used by the design and test organizations.
A 2018 study performed by McKinsey & Co. that looked at 300 public companies over a 5-year period found that those companies that had the best design processes enjoyed 32% more revenue than those companies that didn’t excel in design. These design best practices included the rapid iteration of designs and the testing of those designs to meet ever-evolving customer requirements. One company included in the study was able to bring their products to market 10% faster and generate 30% more revenue by paying attention to their design practices.
Wash, rinse, repeat…
In a rapidly changing environment, your ability to be first to market with a new innovation will drive your revenue – and your margin. If that innovation is for a product that is a durable good with a long life, that innovation will drive your revenue for a long time – or it won’t. In those situations, if you miss the buying cycle and your competitor doesn’t, your company loses for a long time. This makes the need to rapidly innovate, verify design effectiveness, and produce new product offerings critical to your success and the success of your company.
At The Sente Group, our customers are pursuing sales that happen infrequently – missing a buying cycle is costly. This doesn’t mean that rapid innovation isn’t required to keep their customers satisfied. It means rapid innovation is the only way to satisfy their customers. Our customers build platforms that they continually redesign and test – meaning, their test environments are the production environments that feed new product introduction and keep revenue streaming into their companies.
An interruption in their test environments means they risk missing the next buying cycle – which could have a much bigger impact on future revenues than missing the current month’s delivery quotas. The design, creation, and testing of prototypes is the cycle that drives the revenue and health of a company and requires that their traditionally non-production environments be treated like production environments. With the same level of care and urgency as traditional manufacturing environments use to produce inventory. But, traditional manufacturing tools and practices aren’t typically capable of supporting the dynamic complexity found in design environments.
Dynamic Complexity
The challenge for design organizations is their environments are much more complex than their manufacturing environments. This is because design teams are addressing problems with yet unknown solutions. Their needs are more dynamic than a manufacturing organization that is building and testing products with known specifications/tolerances. To maintain these rapidly changing environments requires the same fundamental approach but with tools that can adapt to the accelerated nature of the changes happening in the design environment. Studies in designing for manufacturability show that 8% of a product’s cost is incurred during the design phase and that design affects 80% of total costs. Producing design engineering environments that are readily available to optimize designs is an ongoing imperative for companies that want to compete in today’s marketplace. Standard manufacturing approaches won’t work – they are too static. A new way of thinking with tools that support that approach is required.
Accelerated Enterprise Asset Management
Accelerated EAM has all of the traditional production support tools and practices as any traditional asset management solutions and enables the active management of your environments that can be delivered at the pace required by the environment. This makes it possible to adapt tools to the environment rapidly and continually – as situations change.
Accelerated Enterprise Asset Management makes it possible to standardize your operational and management practices across disparate environments ensuring standards are established, measured, and reported with consistency across your enterprise – freeing you up to take action at the speed required in today’s rapidly changing market. Having these robust practices employed across your enterprise also enables the coordination of resources across functions – producing a resilient network of capabilities that can be used to support itself with greater velocity than each can achieve on their own.
Request a Demo
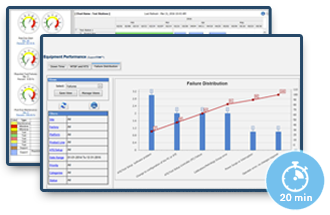
See how Scireo aEAM Software drops asset and support costs by 50% while accelerating time-to-market 2X.
Relevant Content
Covid-19 and The Urgency for Change. Finding & Navigating Dangerous Bumps!
Businesses have been grappling for years with changes in technology and practices driven by the new competitive requirements of the 4th Industrial Revolution (IR4). Then the Covid-19 pandemic appeared and that urgency drove new practices because they were required immediately to continue operations. The pandemic has kicked off a race for improvements and digitization that…
Increase Equipment Utilization, Dramatically Increase Speed
Increase Equipment Utilization: Test Operations are High-Leverage Targets Test’s ubiquitous presence in mission-critical engineering, manufacturing, and MRO processes makes it uniquely high-leverage as a focus for cost containment and process acceleration. It was hands down why one customer-selected test equipment operations as the place to focus. Focus in this area is why another customer delivered…
Notable Quotes
“The Sente Group has saved us millions and made our engineering teams more productive.”
Engineering Manager