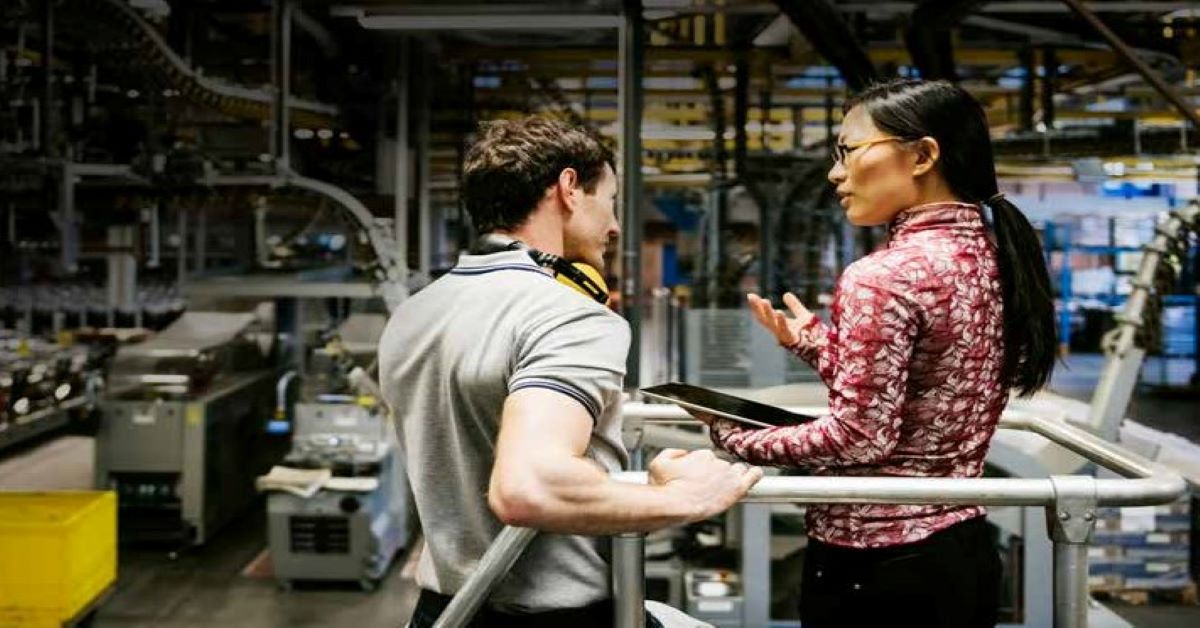

Increase Equipment Utilization: Test Operations are High-Leverage Targets
Test’s ubiquitous presence in mission-critical engineering, manufacturing, and MRO processes makes it uniquely high-leverage as a focus for cost containment and process acceleration. It was hands down why one customer-selected test equipment operations as the place to focus. Focus in this area is why another customer delivered improvements to speed and cost that were 400% greater than the next best improvement project across their entire enterprise.
Dramatic Improvements: One Customer Tells the Story
This customer was concerned with increasing utilization, lowering cost, and increasing speed so they could achieve the growth they knew was possible. The team ultimately achieved results many didn’t think possible. While they successfully doubled company revenues they also…
- Reduced Costs by 50%
- Increased Speed by 35%
- Increased Utilization from 15% t0 over 60%
Listen as our customer explains the successes he achieved at 27:48 of the video, Digital Transformation: Asset Management 5.0. We think if you do you’ll want to watch the rest of the video to see how we partnered with our customer to achieve these results!
The audience was managers and executives attending our talk on Digital Transformation at the 38th Symposium of The International Test and Evaluation Association. The theme of the symposium was, “Evolution of Test and Evaluation in an Age of Rapid Technological Change.”
Other Typical Results:
- 40% reduction in equipment obsolescence
- Non-value added tasks automated or eliminated
- Increased Collaboration
- Less reactive, 70% more planned with contingencies
Improving Test Equipment Operations also Improves Lives
These results are why those who use our aEAM solution to manage their test assets win management awards for the improvements they make. One team even went to Disneyland, and why not. Their management asked them to increase equipment utilization. As their business doubled their asset base was cut in half! Utilization quadrupled. They produced a more satisfying, fun, focused, and innovative work environment that grew and as a result, opened new opportunities for career advancement of the team members.
Leveraging Enterprise Test Assets Requires a Local-Global Approach
For years common asset and property management solutions were used in test operations to produce incremental improvements to asset costs but had a negative effect on speed. These disconnected solutions were incapable of leveraging enterprise assets to produce “one company” benefits across organizations. They failed to increase equipment utilization significantly and wer often a burden on time-to-market. Managing assets is a much different game in engineering than it is in manufacturing or quality where hoarding is a concern. In order to get leverage, the system must be one global system across functions but also be must be tailorable, configurable, and infused with the knowledge that makes each enterprise process resilient.
Increase Utilization with a “One Company” Approach to Leveraging Assets
Our unique capabilities reduce time-to-market and improve profitability. Our software and solutions Connect, Power, and Accelerate your teams by simplifying the already complex asset-intensive environments where they operate.
-
We CONNECT teams and their assets with integrated workflows that create a “whole system” asset management approach, integrating typically stand-alone modules and eliminating the frustration and cost of multiple difficult-to-use systems.
-
We POWER team members by embedding contextual data allowing faster, better, and more trustworthy decisions. Scireo provides data on asset capability and market knowledge along with the contextual knowledge of past use and future planned use enabling quick assessment of constraints and contingency plans.
-
We ACCELERATE teams by leveraging Scireo algorithms to reduce the friction of drag on your teams caused by costly and destructive team behaviors.
aEAM with Embedded Test Knowledge = Test Resource Management
When Scerio aEAM software includes embedded test knowledge we call that solution Test Resource Management. It is a solution that has won numerous customer and industry awards and is unique in the total value of asset management benefit produced.
Request a Demo
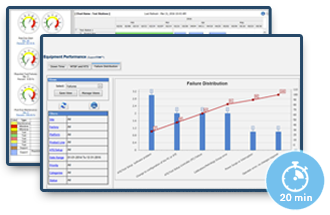
See how Scireo aEAM Software drops asset and support costs by 50% while accelerating time-to-market 2X.
Relevant Content
Asset Management 5.0: Designed for Speed & Competitiveness
Accelerated Enterprise Asset Management (aEAM) is an award-winning software and services suite used by companies with complex, asset-intensive operations and demanding competitive requirements for better than incremental improvements to speed, agility, and cost-effectiveness. The same old solutions won’t work. This is where Scireo aEAM comes in oto help transform your business. The Results with Asset…
Equipment Utilization: What’s your number?
Measuring equipment utilization is the best way I know to determine if your assets are being hoarded and, as a result, if your business is incurring all of the costs associated with it. Hoarding creates the need to acquire equipment that’s not really needed and all of the support costs as well. It also causes…
Case Study: Aerospace Company Drives One Company Synergies
Like many aerospace companies, this one had many sites and different legacy cultures on each. See how they installed common resource management tools, increased utilization 3X and funded new programs.
Case Study: Semiconductor Company Increases Test Equipment Utilization
This company had a leading market share and wanted to solidify its position with its strategic customers by installing test capabilities on their sites. See how a 40% increase in bench utilization funded the project.
Notable Quotes
“While competing companies provide test asset management solutions that offer simple inventory tracking capabilities, Sente focuses on providing a variety of integrated solutions that bring efficiency and effectiveness to test operations and that enable improved alignment with the supply base. Sente’s software tools have improved utilization rates of test assets (with cases using Scireo exceeding 50%), reduced downtime caused by unplanned equipment requests—in some cases reducing lead time from 16 weeks to less than 1 day—with enhanced program schedules.”
Industry Analyst, Frost and Sullivan