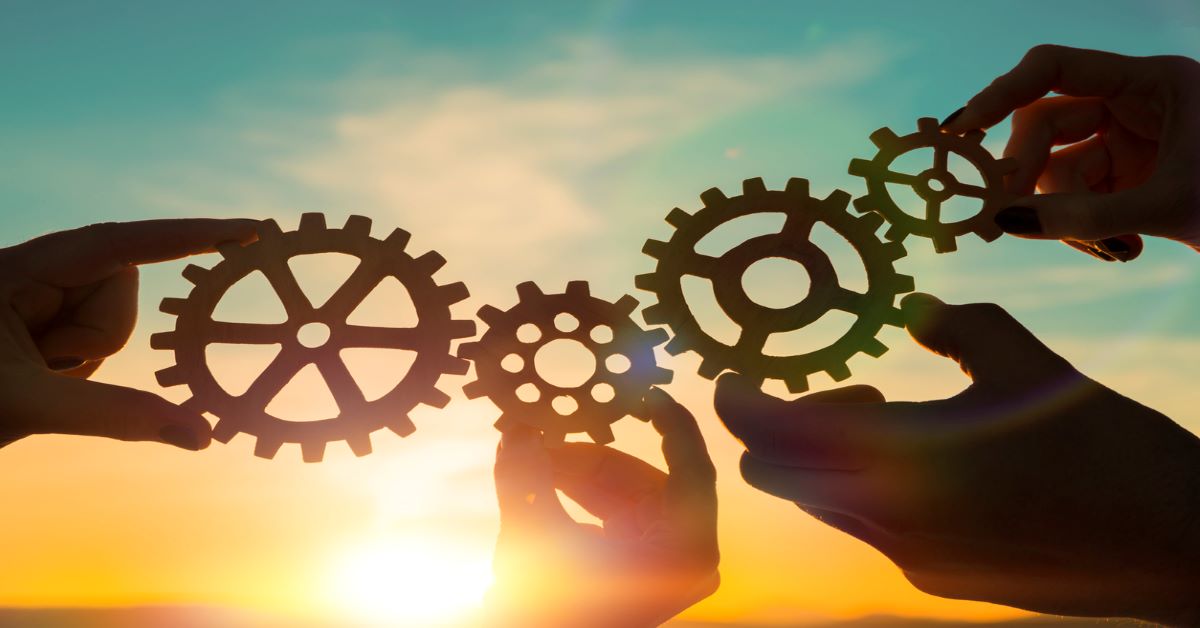

An ongoing critical concern of asset-intensive operations is ensuring the equipment is operational and available to produce output. A company’s revenue depends on it. Profitability is reduced if not managed effectively and the reputation of the maintenance/support teams can suffer.
In a world where we have to learn to go faster and cut costs, old practices hold us back. It doesn’t have to be this way… New aEAM tools and practices help support teams improve responsiveness by 80% and reduce downtime by 30% while lowering overall costs. Support teams satisfy their customer and are recognized for their valuable contributions.
Reactive, Ad Hoc, Siloed, and Without Context
For many organizations the process is reactive. When something breaks everybody responds with heroic efforts to get things back online. But over time they become frustrated by the lack of any real improvement. Maintenance and replacement budgets are constrained or limited because managers simply don’t have the assertions needed to justify the cost of improvements.
Often organizations suffer along with ad hoc or legacy practices & processes – that while they may be well understood, aren’t measured and managed in an integrated way including the full context. For instance, they don’t capture facts or share them easily with other systems – like scheduling – to understand the full context of the maintenance situation quickly to plan and execute to optimize returns on the assets. Support personnel is expected to produce different (better) results, even though they do not have ready access to information tools to enable that – or the tools are multiple and disconnected preventing the ability to view and assess the current situation in the context of all the obligations.
Easy and Quick Access to Information
The first-responders, launched heroically into action, don’t have ready access to the full history of repairs, maintenance, tests used on, configuration (current and historical), who is the expert on this particular system, who are the key constituents and points of contacts for the various support groups, etc. This information is usually available somewhere – but is not “ready to hand” so the maintenance professional can launch, track and resolve the situation as rapidly as possible.
What is needed is a way to intelligently move the approach from reactive and panicked to proactive and planned. To a highly fact-based, coordinated response that makes the situation and everyone’s performance visible and focuses action on the most high-leverage actions.
But how to start & how and what to measure? How to keep the cost of accumulating all this information low?
Address the Current Situation while Capturing Facts to Drive Future Improvement
We have found the best place to start is with the “break-fix” or “reactive” maintenance and support processes ensuring:
- All issues are being captured (we make it super easy)
- Issues are routed to the appropriate support personnel
- Stake-holders are made aware of issues and kept abreast of status (automated escalations are happening)
- The root cause and corrective actions are being captured
- AND drive quick resolutions.
– so that the current situation is well known, and the proactive maintenance plan will flow from fact-based analysis. With Scireo aEAM software, these maintenance workflows layer on top of the asset management information – so every support request links to all existing asset information, the setup configuration, components, history, and available reference materials. This enables rapid access to problem solutions, easy identification of recurring problems, and assessment of business impact.
Then monitoring and improving the process is facilitated by dashboards, virtual visual lab views, automated performer & management notices & reports; keeping everyone clear on the current situation.
Continuously Tuned Maintenance Plans
Once practices are established to ensure that all issues are identified, responded to, and resolved quickly, the focus must shift to the process of reducing or eliminating those issues. Automated metrics keep track of key performance indicators such as response time, return to service times, downtime, MTBF, etc. and enable the teams to focus on the highest leverage improvement opportunities.
This information is a key input into the proactive maintenance plans and helps ensure that the business can make grounded assessments about required maintenance – and isn’t over-investing or under-investing to support throughput or up-time objectives. Having the breakdowns and improvement opportunities in context helps ground the leverage or value of related actions.
Once established, the maintenance plan is perpetually updated and constantly tuned as part of the ongoing process. And, as with the break-fix support process, this planned/proactive process includes metrics, dashboards, and reports.
aEAM Produces a Virtuous Cycle of Improvements
The data from aEAM’s break-fix process informs maintenance teams about the improvements needed in their planned maintenance and then measures to see if those improvements were realized.
Using this approach and the ServiceTRM and SupportTRM modules of our aEAM solution called Scireo, customers have quickly made 85% improvements in response time and 30% reductions in downtime in the first year.
Customers of Maintenance Teams Become Satisfiable
Managers have a better view of their current situation with real facts to inform and justify investment decisions. Support teams are more focused and proactive, customers of maintenance teams feel they are being heard and start to see real changes that improve their ability to get their job done. The level of satisfaction and engagement between maintenance teams and their customers improves and with its equipment performance and costs. Everyone is satisfied.
Sign up for a demo or a first conversation to see how we can be of service to you and your organization.
Request a Demo
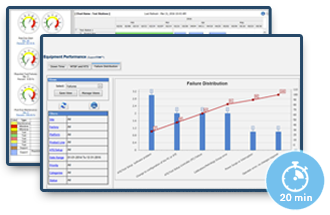
See how Scireo aEAM Software drops asset and support costs by 50% while accelerating time-to-market 2X.
Relevant Content
Every Environment is Someone’s Production Environment
Any complete definition of “Production” must include work that supports the making of some thing or service. That inclusion opens up “production” to include everyone’s work – it really includes your company’s whole supply chain. Wherever work is done is some form of production environment. If that environment (e.g.: computer, truck, instrument, lab space, test…
Customer-Focused Maintenance Teams Accelerate Revenues & Time-to-Market.
Do Yours?
Why are Maintenance Teams so Important? Because they are responsible for keeping plant and equipment up and running so that orders from customers can be quickly produced, shipped, billed and converted to cash. Any breakdown in production inevitably leads to shipping delays, dissatisfied customers, slowed payments, reduced profitability, delays to cash and reductions in stock…
Notable Quotes
“My team’s instantaneous awareness of problem reports with a structured way or recording root-cause and corrective actions allowed for a historical review of data, robust trend analysis, and better lessons learned reduces trouble tickets.”
Factory Support Manager